Phase-change Materials for Cleaner Power Generation
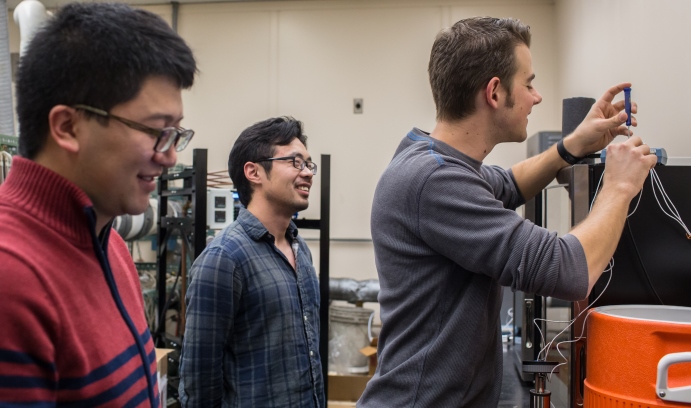
Xingchao Wang (left), Chunjian Pan (center) and Joshua Charles are conducting research in Lehigh’s Energy Research Center on hydrated salts that have the potential to improve the efficiency of power plants that use waterless air-cooled condensers to condense steam.
Joshua Charles, a Ph.D. student in mechanical engineering, has won a competitive award for his research into the use of phase change materials to help improve the efficiency of power plants and reduce the amount of pollutants they emit.
Charles, who is also a part-time research scientist at Lehigh’s Energy Research Center, has received a scholarship from the Air Pollution and Educational Research Grant Program (APERG), which is administered by the Mid-Atlantic States Section of the Air and Waste Management Association.
The scholarship is awarded to doctoral and post-doctoral students who are conducting research related to air pollution and air quality. The title of Charles’s project is “Low Temperature Phase Change Materials for Application Resulting in the Reduction of Airborne Pollutants from Fossil Power Plants.”
Phase change materials (PCMs) absorb thermal energy as latent heat at a relatively constant temperature as they melt. Then as they freeze, they release thermal energy, or heat. Charles is working with hydrated salts, which melt at room temperature and freeze as temperatures drop overnight.
The long-term goal of his research is to help improve the efficiency of power plants that use waterless air-cooled condensers (ACCs) to condense the steam from the turbines that generate electricity.
Thermoelectric power plants boil water to create the steam that spins the turbines to generate electricity. The steam is then cooled back into water and returns to the boiler. The cooling water used in this step represents the largest water withdrawal of the power plant.
Cooling is typically accomplished with cold water, but this poses challenges. Globally, freshwater supplies are dwindling, says Sudhakar Neti, professor emeritus of mechanical engineering and mechanics and one of Charles’s advisers. About two-fifths of fresh water In the United States, for example, is used to cool the steam from power plants.
Second, fresh water is in short supply in arid regions. Third, in “once through” power plants, cooling water is used once and then discharged back into the environment, typically into a river, where its heat can harm fish and other aquatic life.
ACCs use air to cool steam after it powers the turbines. They consume significantly less water than water-cooled power plants but they cool steam less efficiently, especially in regions with high ambient air temperatures. Because of this inefficiency, power plants employing ACCs require more fuel per kilowatt-hour (kWh) of power generated and are thus more expensive to operate.
Charles is seeking to improve the cooling efficiency of ACCs by supplementing them with PCMs. In a lab in Lehigh’s Energy Research Center (ERC), he has built a cycling testing machine that tests 200 grams of hydrated salt, melting and refreezing the material once every two hours for 12 cycles per day. Over a nine-month period, the machine will simulate the effects of eight years of use of the material in a power plant.
Charles is experimenting with several different variations of the salt, adding a nucleation agent in an effort to optimize the performance of the PCM and prolong its useful life in a power plant.
“We’ve done 300 cycles—about a month’s worth—on some of the materials,” he says. “So far, in all three materials, we’ve seen no loss in performance.”
The three-year project is funded by the federal Advanced Research Projects Agency-Energy, or ARPA-E. Lehigh is a subcontractor on the grant, which was awarded to Advanced Cooling Technologies of Lancaster, Pa. The University of Missouri is also participating. ERC director Carlos Romero and Neti are the project’s principal investigators at Lehigh, which is overseeing material development and corrosion testing. Several other Lehigh students are working on other aspects of the project, including graduate students Xingchao Wang, Chunjian Pan and Fengxiang Nie and undergraduate Anika Chakravarti. The ERC maintains research projects in clean fuel utilization, power plants, energy efficiency and pollutant emissions control, renewable energy, and crosscutting technology research and development.
The researchers hope to scale up the PCM cooling technology that Charles is testing, building first a 1-kWh prototype and then a 200-kWh prototype before testing the final product in a power plant.
The goal is to develop PCMs that take heat from the steam after it has passed through the turbines, store that heat during the day and then reject, or release it at night, when air temperatures fall.
Charles earned an M.S. in mechanical engineering from Lehigh in 2011 after completing a B.S. in physics from Mansfield University of Pennsylvania.
His previous research at Lehigh was related to the nationwide efforts to reduce pollution from coal-fired power plants. For his M.S. thesis, Charles investigated the capture and sequestration of carbon dioxide, a greenhouse gas emitted by power plants. He also completed a project with Air Products and advised utility operators in North Dakota and Virginia.
Story by Kurt Pfitzer
Photos by Christa Neu
Posted on: