Electrochemically-produced Ammonia Could Revolutionize Food Production, Researchers Say
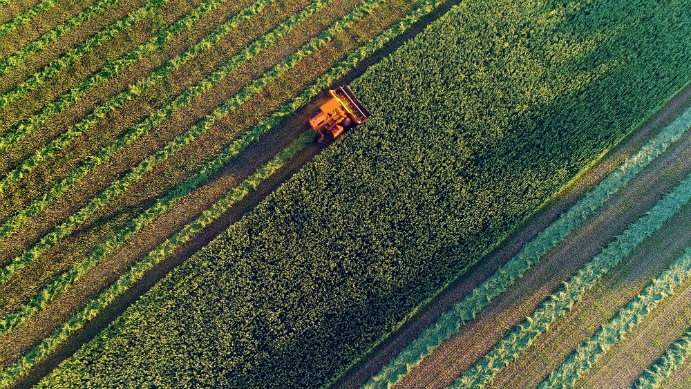
Photo: iStock/JamesBrey
Steven McIntosh wants to transform the way ammonia is produced. He hopes to create a viable alternative to the conventional method, which uses massive amounts of energy and emits harmful carbon dioxide. He’s exploring a sustainable electrochemical method to efficiently drive the chemical reaction that produces ammonia.
Ammonia, a colorless gas made out of one nitrogen and three hydrogen atoms, is found only in small quantities in nature. Large quantities of ammonia are produced through what is known as the Haber-Bosch Process—created by German chemists Fritz Haber and Carl Bosch in the early 20th century. It is credited with making mass food production possible, as ammonia’s main industrial use is in agriculture as fertilizer.
The Haber Process, as it’s widely known, combines nitrogen from the air with hydrogen derived from natural gas—comprised mostly of methane—in a chemical reaction that operates at very high pressure. In this conventional method, Iron, the catalyst used, easily “breaks” the hydrogen atoms. However, a huge amount of pressure is required to “push” the nitrogen onto the catalyst to spur the reaction. In addition, the process of generating hydrogen from methane emits large quantities of the greenhouse gas carbon dioxide into the atmosphere.
Ammonia manufacturing consumes 1 to 2 percent of total global energy and is responsible for approximately 3 percent of global carbon dioxide emissions.
According to McIntosh, the need for increased food production as a result of population growth—2 billion people will be added to the planet by 2050—means there is an increased urgency to find a sustainable method of producing ammonia.
McIntosh puts it more succinctly: “The process of producing ammonia is critical for human survival, hasn’t changed in more than one hundred years and is a big polluter. It’s time for a change.”
McIntosh, a professor of chemical and biomolecular engineering at Lehigh, is exploring a method of producing ammonia that could spur such a change by using electricity to drive the chemical reaction. His method would eliminate the need to use high pressure to break the nitrogen bonds. And, because it derives hydrogen from water instead of natural gas, there would be no carbon dioxide emissions. It’s main byproduct would be oxygen.
McIntosh was recently awarded a three-year collaborative research grant by the National Science Foundation (NSF) to support this research. McIntosh will lead the Lehigh team as principal investigator in close collaboration with a team at the University of Pennsylvania, which includes Professors Raymond J. Gorte, John M. Vohs and Aleksandra Vojvodic.
In a transformative paradigm shift McIntosh and his colleagues will investigate a method of producing ammonia from hydrogen and nitrogen using a proton-conducting, ceramic, solid-oxide electrochemical cell. Their central hypothesis is that atmospheric-pressure, ammonia synthesis can be realized by electrochemically driving hydrogen onto catalytic surfaces that are normally limited by high nitride coverage.
“We plan to experiment using different catalysts, such as Tungsten, that would normally be covered in nitrogen, upsetting the balance of hydrogen and nitrogen that is required for the reaction to take place,” says McIntosh. “We will resolve this imbalance by applying an electrochemical potential to drive the hydrogen onto the catalyst surface and form ammonia.”
The project will take advantage of the infiltration methods previously developed for electrode synthesis in Solid Oxide Fuel Cells, which allows a wide range of materials to be used for the electrodes. The team will also explore mixed electronic-protonic conductors that can be added to the electrode to enhance the three-phase boundary where the electrochemical reaction can occur. The choice of electrocatalysts will be guided by complementary theoretical studies.
McIntosh describes the proposed method as adding an “additional knob”—electricity—to the ammonia production process.
“In this method, the hydrogen will come from water, making it a kind of ‘reverse fuel cell,’ says McIntosh.
A fuel cell combines hydrogen and oxygen to make water, and in the process, creates electricity.
The proposed reactor will utilize electricity to split water to provide the hydrogen required in ammonia synthesis, removing the need to consume natural gas and emit carbon dioxide. This project will result in small-scale demonstration cells that separate the hydrogen and oxygen atoms that make up water, using the hydrogen and emitting the oxygen.
According to McIntosh, researchers have tried similar ammonia production methods but were able to produce very little ammonia. When it comes to ammonia, the ability to produce it at industrial scale is what matters. That is why one of the main goals of the project, according to McIntosh, is to produce a reasonable rate of ammonia production. Another goal is to demonstrate what McIntosh says is the potential “modularity” of this technique.
Ultimately, says McIntosh, this new way of producing ammonia could be part of a larger effort to make food production greener and more sustainable.
“Making ammonia by the conventional method requires a huge energy source, which means it must be made in one location and then shipped—adding to the method’s inefficiency,” says McIntosh. “The hope is that someday ammonia could be produced on-site using a modular cell like the kind we are exploring, powered by a local electricity source such as solar panels or wind turbines.”
Posted on: